Over the last decade, since the introduction of the concept of modular instrumentation based on the PXI platform, the advances in commercial technology & integration of PC software has driven the advances in the modular instrumentation. T&M vendors like Leading T&M vendors are providing user-programmable FPGAs to allow the users to implement custom real-time analysis and complex triggers with no dead time (missed signals) because every acquired data point can be analyzed in real time on the instrument’s FPGA. FPGAs are high-density digital chips that you can customize to directly incorporate custom signal processing and control algorithms into measurement hardware. The result is off-the-shelf hardware that has the best of both worlds—fixed, high-quality measurement technology; the latest digital bus integration; and user-customizable logic that is highly parallel, provides low latency, and is tied directly to I/O for inline processing and tight control loops. While user-configurable FPGA instrumentation is still a new concept in the marketplace, this trend to providing user-programmable FPGAs on instrumentation produces both substantial challenges and new opportunities for innovation.
Historically, one could only program an FPGA using a relatively low-level hardware description language (HDL) such as VHDL. But today, one of the most important innovations in the FPGA community involves providing abstraction software to simplify the programming of the FGPA. National Instruments offers full access to the instrument I/O and analysis logic with a suite of software tools for non-HDL programmers. LabVIEW FPGA allows users to use a graphical programming approach to implementing logic on the FPGA to define the behavior of an instrument in hardware and reprogram the instrument when requirements change. The graphical data flow nature of LabVIEW is well suited for implementing and visualizing the type of parallel operations that can be implemented in digital hardware.
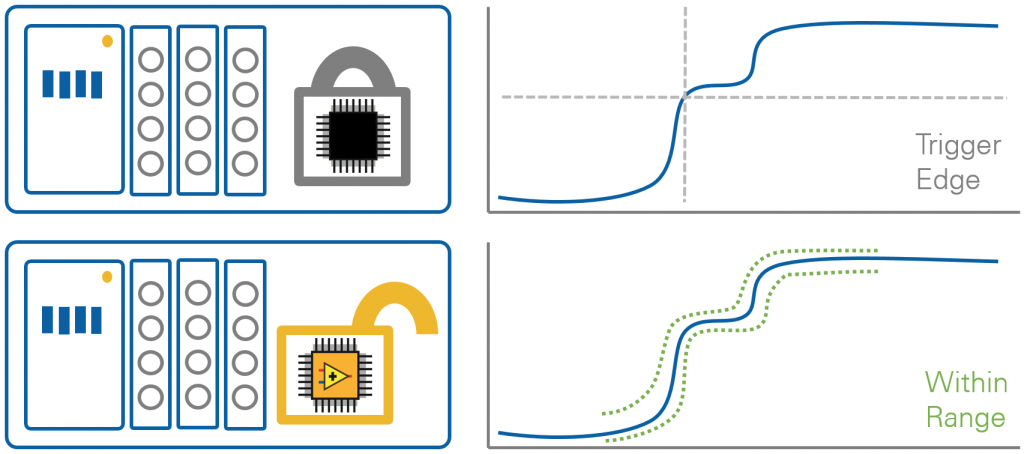