Most resin systems in use today are extremely complex products with elaborate chemical formulations. Process characteristics and final properties are usually adjusted by the manufacturer to suit the customer’s requirements, and this necessitates a great deal of skill, knowledge, and experience. And yet resin technology is an often-overlooked area in electronics manufacturing. Over the past few years, there have been a number of major developments in material formulation and utilization that have resulted in extremely effective new products being brought onto the market. Epoxy resins are the long-time favorites for potting and encapsulation, but with formulators rapidly reaching the limits of what can be achieved with these materials, they have turned to polyurethane chemistry. So, in this month’s column, I’m going to look at polyurethane-based products that are fast becoming the resins of choice for those requiring high performance with cost-effective pricing.
What are the key differences between PU and epoxy encapsulation resins?
The main difference between the two would be flexibility and hardness; epoxies tend to be much more rigid and tough than polyurethanes, offering excellent sealing and ingress protection to the assemblies they are encapsulating, while polyurethanes are usually a little softer and more flexible, which can often make them more forgiving when considering stresses on delicate components during thermal cycling.
These differences can also influence the temperatures the resins are suitable for. For instance, epoxies are not typically suitable for temperatures below -40°C as they become too brittle, while polyurethanes can be suitable for temperatures as low as -60°C. At the top end of the temperature scale, polyurethanes are only suitable up to approximately 130°C, or 150°C in exceptional cases (such as our UR5645), whereas epoxies can be pushed higher, above 200°C.
Have you ever been convinced that an epoxy would be the best solution, but a PU resin won the day?
This isn’t something we typically see when we work with a manufacturer from the outset. Usually, it is clear once we have collaborated with them to identify their key requirements and end-use parameters to assess which chemistry would be best. In fact, we are often able to narrow it down to one or two specific resins to take to the testing stage. However, it is something that we have seen in the past when a manufacturer has chosen a resin for themselves without any of our specialist input and finds that their resin choice is not working well in the field. By way of an example, an EMS was potting remote vehicle unlocking units for an OEM and had self-selected an epoxy for their units. Once the units reached the thermal cycling stage of approval testing, it was found that many units were failing, and further investigation revealed that this was because components were being pulled off the board. What was happening here was the rigid, inflexible epoxy was adhering well to the assembly but expanding and contracting to a different degree than the board and components due to a CTE difference, which was causing so much stress that the solder joints were breaking. We recommended that they test our UR5604 resin instead, which is a tough but flexible polyurethane, and they found when they used UR5604 they saw no failures during thermal cycling as this was able to flex better with the assembly during rapid temperature changes.
Do you have a ‘most popular’ resin and why is this?
This is a tricky one, many of our resins are very popular, but if I had to highlight specific resins it would be our general-purpose ER2188 and UR5604 because they are excellent “all-rounder” resins. ER2188 is a tough and rigid epoxy, while UR5604 is a more flexible polyurethane, although still tough enough for many environments. Both are flame retardant, to UL94 V-0 level, and have a good level of thermal conductivity to allow for heat dissipation away from hot spots in the assembly. Unlike many other resins with good thermal conductivity, they have excellent flow, allowing them to be used even in tightly spaced units that need the resin to flow into small gaps. Both resins offer excellent electrical performance and dielectric strength, and excellent general environmental protection. All of these properties make them an excellent starting point for many applications.
In the early days of potting and encapsulation, epoxy resins were certainly the materials of choice. But with epoxy resin technology having tended to mature over recent years and most of the exciting developments in resin technology now taking place in polyurethane chemistry, use is gradually switching across. Polyurethane resins are now becoming more and more dominant and taking market share from epoxies to an increasing extent. Please do contact one of our Technical Support team to learn more about how resins can be implemented into your application.
Authored Article by:
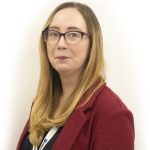