Courtesy: Siemens
Are you familiar with this situation? You have been using a smartphone from the same provider for many years. Every icon, every gesture, every update – everything seems familiar to you. But one day, your employer gives you a new company phone, this time from a different provider with a different operating system. You take it out of the box and immediately notice the change. The home screen looks different, the settings aren’t where you expect them to be, and even simple functions like sending a message or setting up your email feel complicated. You spend hours familiarizing yourself with this new system, an experience that is not only frustrating but also time-consuming.
We face similar challenges in industrial manufacturing, especially when it comes to integrating machines from different manufacturers into a single production line. Different operating systems not only make familiarization difficult, but also networking within the production lines. This is where standardization comes in: Uniform operating concepts and interfaces, for example, make handling easier and enable efficient data communication. This leads to smooth integration and increases the overall efficiency of the systems.
Industrial Ethernet: The basis for digital factories
Let’s assume that you are responsible for the design of a new production line in which machines from different manufacturers have to be seamlessly networked with each other. You will have to delve deep into the technical details of each individual machine and its interfaces.
Did you know that there are over 70 different industrial protocols? Just think of how much time you would need to ensure that everything works together smoothly. And have you thought about monitoring all your machines from one central location? This could give you a clear picture of what’s going on in your production. Also, don’t forget to make sure that all your machines can communicate with each other securely.
That’s why communication standards are becoming increasingly important to enable data exchange between machines. Our solution for this is the use of two proven Ethernet standards: PROFINET and OPC UA. This combination creates a consistent, manufacturer-independent communication platform that enables the smooth integration and operation of different machines and systems. These standards not only reduce training times, but also increase overall efficiency.
From horizontal to vertical integration
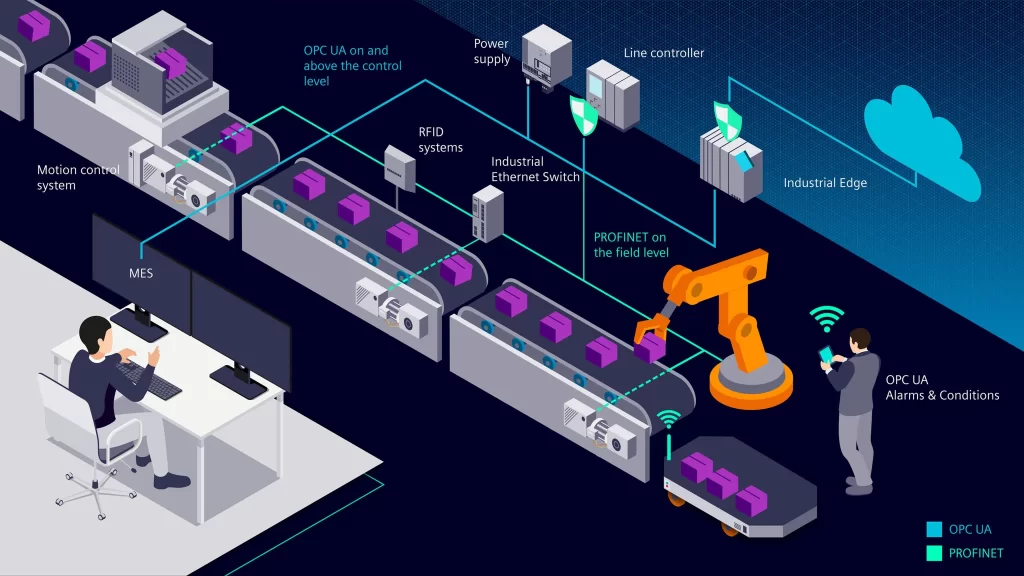
Like a smartphone that synchronizes data with the cloud, ensuring that photos, contacts and documents are accessible anytime and anywhere, standardization in the industry ensures a smooth flow of data between the production machines (horizontal) and the higher-level corporate IT systems (vertical). This sophisticated integration enables production processes not only to be monitored, but also actively controlled and optimized.
This seamless network between machines and management levels is crucial for modern production facilities. It enables them to maintain full control over their processes while maximizing efficiency and productivity. In practice, this means that data flowing horizontally between machines on the shop floor and information flowing vertically to decision makers together form a dynamic system that can react quickly to changes. This system forms the backbone of a smart factory, where every component and every process is perfectly aligned to achieve maximum efficiency and productivity.
Our approaches to modular standardization, which include both horizontal and vertical integration, enable quick adaptations through consistent machine engineering and accelerate the development of new production lines. This saves time by using components that are already available.
The standardization of operating concepts not only reduces the training time for employees, but also increases the efficiency of engineering. Tools such as the Faceplate Library and the Corporate Designer reduce effort and minimize errors through the use of proven content.
Efficient production monitoring
Standardized safety and diagnostic systems ensure seamless monitoring of the machines. These systems react immediately to irregularities and thus prevent production downtimes, while at the same time optimizing the operating process. Their comprehensive data analysis and communication not only protect the physical safety of the systems, but also the integrity of the production data.
Thanks to OPC UA and its Alarms & Conditions specification, diagnostic information from SIMATIC S7-1200/1500 controllers can also be used in devices from other manufacturers. This transparency increases flexibility and enables technical personnel to receive error messages directly on mobile devices and react quickly. The robust security functions of OPC UA, including authentication, authorization and encryption, guarantee the highest security standards.
A holistic approach to mastering complexity
Standardization is more than just a tool for increasing efficiency – it is an engine for innovation. By standardizing interfaces and processes, we create modular and scalable systems that accelerate the development and market launch of new machines and enable rapid adaptation to changing market requirements and technological advances.
The use of advanced standards such as PROFINET and OPC UA simplifies the integration of different systems and guarantees the highest safety standards.
For deeper insights into the benefits of standardization, I recommend taking a look at our white paper. It not only provides a comprehensive overview of the technical details and their practical implementation, but also shows how standardization can help to master complexity, shorten time-to-market and increase productivity in order to operate more efficiently, cost-effectively and error-free than the competition.