The new century ushered in a lot of technological advancements. Among them is the evolution of new energy vehicles that have flattered mobility. The emerging trend of new energy vehicles has seen an evolution. Since the very beginning of the century, sales of new energy vehicles have increased many folds. This has impacted the large-scale production of vehicles throughout the globe. This continuous usage of the battery has ushered into the peak period of power battery scrapping of new energy vehicles. Here concerns arise about the disposal of these power batteries. Thus, this article will be circling around the disposal of the batteries used in new energy vehicles.
As a fact known globally, automotive power batteries, whether ternary lithium batteries or lithium iron phosphate batteries are recycled, there are only two scenarios, by which they are restored. One is trapezoidal utilization and the other is material regeneration. The trapezoidal uses the battery for secondary use, such as the car power battery being scrapped, and it can be used in a toy car to continue to be used. When the capacity of the car’s power battery is reduced to about 80%, the car’s endurance cannot meet the normal demand. After the company recycles, the battery cells are removed and continue to be used in other aspects. When the battery capacity falls further, recycling is the final destination of the battery, through dismantling and separation, and even purification, entering a new production line and starting the next cycle.
Some researchers say that the cumulative decommissioning of power batteries globally is about 200,000 tons, of which large quantities flow into informal channels such as small workshops, bringing hidden dangers to the environment and safety. It is reported that a 20-gram mobile phone battery will pollute a square kilometer of land, which will pollute for about 50 years. The car’s power battery will cause greater damage to the environment.
Moreover, the acquisition of recycled batteries by small workshops at a low price disrupted the normal business order of the market and made the previous battery recycling industry very chaotic. In contrast, the material regeneration method is better, such as the disassembly of used batteries, as well as the fragmentation and separation of materials, and the remediation or smelting of resources. Take common ternary lithium batteries as an example. There are many non-ferrous metals such as manganese, nickel, and cobalt. They can be used for a long time until the battery attenuates to less than 30% of the initial capacity, and some of the metal elements in them can still be recycled. In particular, cobalt and nickel are very scarce mineral resources, but the battery recycling process is very complex and the cost is not low. First of all, the battery should be fully discharged. Then split various materials inside the battery, such as diaphragms and electrolytes, as well as positive and negative electrodes, remove parts of the materials, and finally smelt and recover metal elements.
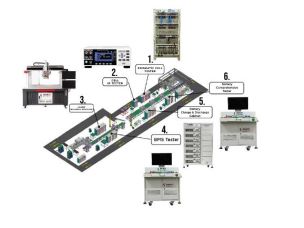
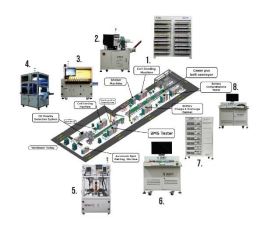
The write-up is authored by Neeraj Kumar Singal. Founder and CEO of Semco Group. He is passionate about Clean Energy and working on various projects to build a robust Lithium-ion ecosystem. He can be reached at nks@semcoindia.com