Industrial Automation has always been part of manufacturing industry on limited basis. Over the past few decades automation has become a necessity in manufacturing industry due to global competition. This has helped in efficient manufacturing processes and in mass-production of goods. Automation is becoming inevitable globally in the manufacturing industry today.
Automation in its broadest sense has expanded from its original industrial manufacturing base to laboratories and businesses. The application of robotics and automation has been successfully achieved in a wide range of industries dealing with well-defined processes and productsfrom the manufacturing , FMCG, automotive , the healthcare , the pharmaceutical Some of the challenges in the application of robotics and automation in the manufacturing sector include large upfront investments in hardware and software, as well as the costs of workforce training and education. Industrial robots need sophisticated programming, and while the number of people with this skillset is growing, it’s currently limited. Programmers are in short supply and paid well, so it’s important to also consider the personnel investments manufacturers need to make in expertise. While robots reduce some labour costs, they introduce other ongoing expenses, such as preventive maintenance, troubleshooting and programming. As for any new field, robotic scientists are developing many components on spec. So that robots may become more accessible, some components will become standard and will be mass-produced at low cost.
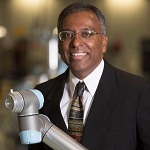
With the idea of higher production rate and the need for human interaction with machine automation, the Collaborative robots were first developed in 2008 by Universal Robots (UR). Their latest technological advancement in collaborative robots or ‘Co-bots’ was brought out in the international market with a peculiar intention which is in line with Industrial 4.0; which is in sync with the automated revolution in the manufacturing industry.
Cobots have already made inroads on the assembly line, performing a variety of simple tasks with minimal human intervention. These machines can be used for quality control purposes, such as detecting the presence of defective or non-standard products and removing them from the line. They can also test circuit boards, load pallets, apply paint, and affix or tighten small objects. Cobots can accomplish simple tasks and they can operate well in temperatures that would be uncomfortable people.
UR’s UR3, UR5 and UR10 can incorporated into various processes so that engineers could easily adapt software to specific needs for required tasks. The easy programming, installation and collaborative nature of the industrial robot arms allow them to work side-by- side with workforce.
They can be programmed by operators adding tremendous flexibility to meet human problem-solving needs. Cobots give manufacturers the opportunity to grow in measured steps so they can maintain competitiveness in a global landscape. Cobots are ‘third hand’ that helps the workforce in carrying out monotonous tasks, as UR believes in giving back power to the worker. They can be seen as a step forward in widening the scope of Indian manufacturing industry, not only in quantity but also quality.
The technology of cobots continues to evolve. Cobots will make inroads into other fields, industries as their range of capabilities broadens and enables them to perform tasks barely imaginable today.