Author: STMicroelectronics
STPOWER Studio 4.0 just became available and now supports three new topologies (1-phase full bridge, 1-phase half-bridge, and 3-phase 3-level T-NPC) to cover significantly more applications. Previously, the online simulation tool only offered a 3-phase 2-level topology for motor drivers and photovoltaic inverters, which are some of the most popular use cases. Thanks to the robustness of the underlying architecture that ST recently updated and brought to the web, we are now able to build on top of the existing platform to make STPOWER Studio more versatile and assist more engineers in designing a more comprehensive range of power stages.
What is STPOWER Studio?
A unique simulator
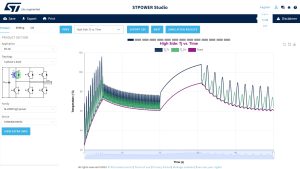
STPOWER Studio, a component of eDesignSuite, specializes in thermo-electrical simulations. As eDesignSuite transitioned to HTML5 to enhance its user interface, STPOWER Studio benefited from the same underlying architecture, enabling more powerful simulations. It stands out in the industry as one of the few simulators capable of adjusting power losses according to the junction temperature at the moment of the simulation, providing a more accurate representation of real-world usage. Some competitors traditionally use a fixed value for the junction temperature, leading to over- or underestimated losses. Thanks to our dynamic junction temperature, users get more accurate results.
STPOWER Studio can simulate up to hundreds of seconds per step with Steady State
off, which gives engineers enough time to see how their power stage would ramp up and stabilize. They can also run simulations with or without heat sinks, which will help them anticipate form factor and heat dissipation requirements. Users simply select the ST family of devices (ACEPACK or SLLIMM) and the component they will use in their design. Under Setting
, designers can tweak the gate resistor values and some thermal properties. Finally, under I/O
, users can adjust their mission profile by defining various steps with values such as the output power or the current level, among other things.
A design assistant
Let’s take the example of an engineer designing a large motor driver for industrial applications, an inverter for a photovoltaic converter, or an HVAC system. In our example, the motor would use a DC Link voltage of 650 V and an RMS Phase Current of 10 A. For a quick simulation, users can use Steady State
ON to analyze performances after reaching a thermal steady state. Then, by choosing Steady State
OFF, users can set the duration of the simulation step for a more detailed analysis. Obviously, it will require more computing power on the server and take longer to generate. However, ST reduced rendering times by a factor of 10 over the last releases of STPOWER Studio.
What’s new in STPOWER Studio 4.0?
1-phase full bridge
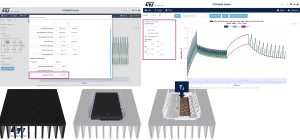
The new version of STPOWER Studio features three new topologies. The 1-phase full bridge will fit single-phase photovoltaic converters or uninterruptible power supplies. As more residential homes and buildings increasingly rely on renewable energy, the ability to store solar energy in batteries is increasingly in demand. Hence, we wanted to ensure that engineers could more rapidly test their designs and reduce their time to market. Similarly, engineers working on an uninterruptible power supply can very quickly anticipate what their design will look like if they adopt an STPOWER device.
1 phase half bridge
Since STPOWER Studio supports a one-phase full bridge topology, it made sense to offer a one-phase half-bridge. This structure is common in DC-AC conversion for smaller solar inverters or motor drivers. Engineers also combine single-phase half-bridge topologies when designing a one-phase to three-phase converter. In fact, while the current version of the simulator focuses solely on DC-AC systems, we are evaluating the addition of DC-DC applications and will update this blog post with more information as they become available.
3-phase 3-level T-NPC
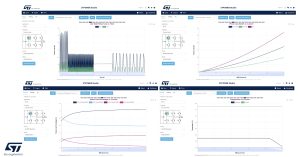
Finally, the 3-phase 3-level T-NPC (T-type Neutral Point Clamped) is increasingly popular because it improves overall efficiency by reducing switching losses thanks to a mechanism that clamps the input voltage at its halfway point. Consequently, only half of the input voltage is applied to each switch, which reduces switching losses. This creative approach greatly benefits high-power systems, such as photovoltaic inverters, power factor inverters, or motor drivers, while ensuring the overall design remains relatively small.