In a world fast moving towards the Internet of Things and initiatives like Smart City and Smart Building, with ever-growing dependency on electronics in our day to day works, predictive maintenance becomes a necessary & helpful tool to minimize disruptions. Predictive Maintenance techniques detect anomalies in equipment before those turn into system-critical failures, allowing maintenance to be scheduled before the equipment actually breaks down. In contrast to preventive maintenance which is characterized by regular inspection intervals for maintenance replacements and repairs, predictive maintenance can detect system failures outside of set maintenance intervals. This increases equipment uptime reduces overall maintenance costs and allows optimization of spare part inventory by enabling preventive maintenance based on the equipment’s actual needs.
– The latest measures to enhance the efficiency in predictive maintenance.
- Infineon recently developed the XENSIVâ„¢ Predictive Maintenance evaluation kit to enable their customers to easily and quickly evaluate predictive maintenance functionalities in their system. Thanks to the evaluation kit, customers can reduce their time to market and engineering efforts.
The XENSIVâ„¢ Predictive Maintenance evaluation kit includes pre-selected hardware (sensors, microcontroller, embedded security) as well as software for condition monitoring and anomaly detection and CloudFormation templates. Infineon worked together with IoT service provider Klika Tech and is powered by cloud service provider AWS to create an end-to-end solution for customers to facilitate and boost the adoption of predictive maintenance features.
– The application of sensors as predictive maintenance.
In predictive monitoring, constant monitoring of system performance and state anticipates potential failures outside the planned inspection intervals of preventive maintenance. However, leveraging the potential of predictive monitoring can require what is referred to as condition monitoring. Condition monitoring is a prerequisite for predictive maintenance and as such is a component part of predictive maintenance, not a maintenance strategy in itself. Condition monitoring can be compared to an employee who constantly monitors a system’s condition and records any irregularities during operation but does nothing more.
- Sensors are the backbone in the data collection process of condition monitoring and predictive maintenance. Placed inside systems, they collect data on the most crucial system parameters such as current, vibrations, sound anomalies, airflow and many others. Combined with microcontrollers, connectivity and embedded security, collected data can be processed to detect anomalies before they turn into costly failures.
Here, a variety of sensors can be implemented such as current sensors, 3D magnetic sensors, pressure sensors, MEMS microphones and hall sensors and switches:
- Airflow measurement at the compressor based on the XENSIVâ„¢ DPS368 barometric pressure sensor
- Current measurement at the fan and compressor based on the XENSIVâ„¢ TLI4971 current sensor
- Position sensing of the motor with XENSIVâ„¢ TLI493D-A2B6 3D magnetic sensor
- Sound anomaly detection in the unit with the XENSIVâ„¢ IM69D130 MEMS microphone
- Linear vibration measurement with XENSIVâ„¢ TLE4997E Linear Hall sensor
- Opened and closed lid detection with XENSIVâ„¢ TLE4964-3M Hall sensor
- Speed and direction measurement with XENSIVâ„¢ TLI4966G Double Hall sensor
- Data processing with XMC4700
- Secured connectivity on and authentication with OPTIGAâ„¢ Trust M
– discuss the technical specifications for sensors by your company for predictive maintenance.
- Infineon offers a broad range of highly accurate sensors for reliable and precise data collection
- XENSIVâ„¢ DPS368
- Miniaturized absolute digital barometric air pressure sensor with temperature sensor
- Ultra-high precision (±2 cm) and low current consumption
- Environmentally resistant package: Protection against water, dust and humidity
- XENSIVâ„¢ IM69D130 MEMS microphone
- High-performance digital MEMS microphone
- Noise-free audio raw data: 69 dB[A] signal to noise ratio
- Distortion-free audio signal: <1% total harmonic distortions up to 128 dBSPL
- XENSIVâ„¢ TLE4997E Linear Hall sensor
- Highly accurate Linear Hall sensor qualified for harsh environments up to 150°C
- Ratiometric analog output
- XENSIVâ„¢ TLI493D-A2B6 3D magnetic sensor
- Highly accurate 3D magnetic Hall sensor for industrial applications
- Magnetic field range: +/- 160mT
- Broad microcontroller compatibility
- XENSIVâ„¢ TLI4971 current sensor
- High precision miniature coreless magnetic current sensor for AC and DC measurements
- Analog interface and dual fast over-current detection outputs
- High accuracy over temperature and lifetime
- XENSIVâ„¢ TLE4997E Linear Hall sensor
- Enables highly accurate rotation and position detection
- Programmable linear hall sensor
- High linear and ratiometric push-pull rail-to-rail output signal
- Digital temperature compensation
- XENSIVâ„¢ TLE4964-3M Hall sensor
- Highly accurate integrated Hall-effect switch
- Superior supply voltage capability
- Wide operating temperature range and temperature stability of the magnetic thresholds
- XENSIVâ„¢ TLI4966G Double Hall sensor
- Double Hall switch with two output pins with direction & speed information
- Operation from unregulated power supply
- Superior temperature stability
- XENSIVâ„¢ DPS368
Authored Article by:
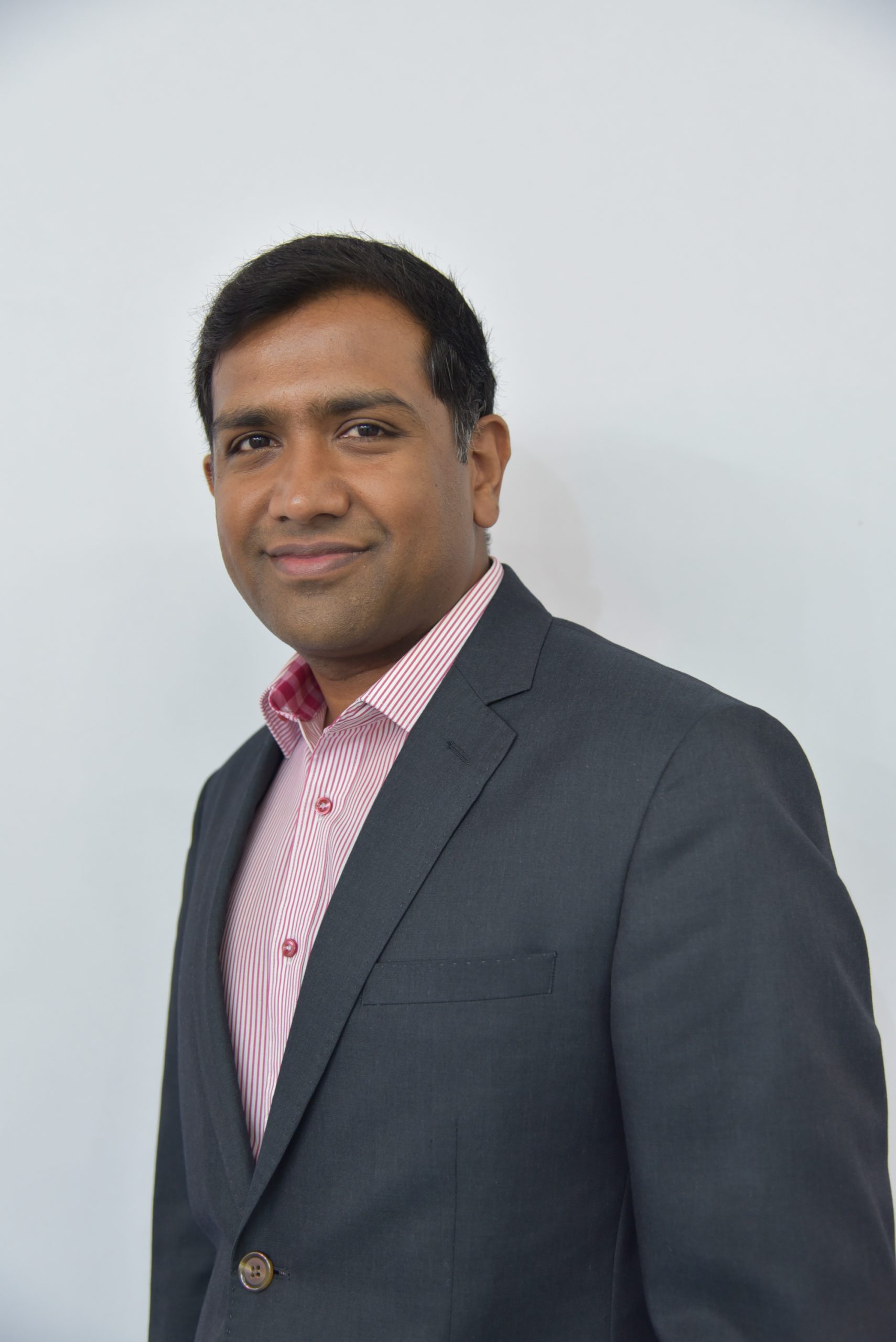