The aerospace industry in India is one of the fastest growing sectors with an increasingly strong domestic manufacturing base. To gain further competitive advantage, the implementation of new technologies such as additive manufacturing has been gaining importance in the recent past. While this method leads to cost reduction of building low-volume parts, as well as enables the industry to challenge the limits of efficiency through extremely accurate and complex design executions, the quality challenges faced by this new manufacturing processes should also be thoroughly addressed. High-precision metrology solutions are not only an opportunity to optimize the manufacturing process but also offer valuable insight for material sciences and ensure the quality of the output.
Additive Manufacturing as an Opportunity in Aerospace
Air travel, a preferred mode of transportation, relies on aircraft parts meeting stringent quality standards. For instance, before a supplier commences production, up to 1500 inspection features of a turbine blade must be verified, adhering to tight tolerance ranges at every production step. Beyond this challenge, another is the vital maintenance and repair operations (MRO) which often involves replacing high-complexity, quality-intensive low-volume or single parts. Traditional manufacturing processes for MROs prove both time and cost-intensive, unable to meet the demanded complexity and accuracy efficiently. Consequently, additive manufacturing, specifically 3D printing, is increasingly integrated into the aerospace production chain in India, positioning the industry as a pioneer in additive manufacturing innovation. However, the adoption of this technology brings its own challenges, which our experience suggests can be effectively addressed through high-quality metrology solutions.
Hitting the Brake: The Process and Challenges of Additive Manufacturing
Powder is the building block of additively manufactured parts. The particles are small, typically ranging from a few micrometers to tens of microns in diameter. Their size distribution and shape influence spread ability and hence possible defects might occur during the process. The defect density is among other aspects and also a factor for recycling and aging of the powder. A uniformly distributed powder bed is the essential basis for a stable and reliable additive manufacturing process. Improper powder quality, powder rheology and the process parameters might cause voids to form in the final structure. The additive manufacturing process, unlike traditional manufacturing methods, requires powders to be melted layer by layer during the build. Melt temperatures and process parameters greatly affect the crystallography and, as a consequence, part properties. After printing, the part is still attached to the build plate. It is then heat-treated for stress relieving and removed from the build plate with a band saw or wire EDM. Some parts are then heat treated again for microstructure changes. These processes possibly influence the characteristic and accuracy of the part, impacting the quality and safety. Post which, Dimensional accuracy and surface finish are critical to ensure proper assembly and consistent matching across multiple parts. Even though additive manufacturing is an immense opportunity since it enables an unprecedented control over material microstructures. Analyzing and understanding these structures is key for an efficient and optimized process that ensures the demanded quality and safety.
Precision at all Altitudes: Overcoming the Challenges
Utilizing cutting-edge measurement and inspection equipment is crucial for meeting aerospace parts’ sophisticated requirements. Our metrology solutions support and can be implemented throughout the manufacturing process, enabling immediate corrective actions, ensuring high-quality output, and promoting sustainable resourcing. We employ Light or Electron Microscopes and CT for continuous powder characterization, identifying sources of quality issues in the powder bed during or after printing. Defective parts can be detected and fixed during the build, avoiding downstream costs and increasing yield. Optical 3D-scanners, Coordinate Measuring Machines, and high-resolution CT validate accuracy, inspect finished parts, and analyze internal structures, contributing to defining optimal settings for future processes. The comprehensive data analysis across the process chain, facilitated by metrology devices equipped with IoT and PiWeb software by ZEISS, ensures correlation and supports an efficient and optimized process. Investing in high-quality metrology and research equipment is indispensable for ensuring safety and quality in the aerospace industry, particularly as ‘Make in India’ propels the sector’s growth, with additive manufacturing playing a vital role in material science and process optimization.
ZEISS, as a key global provider, plays a pivotal role with its Blue Line process, contributing to the industry’s success through precise metrology and quality solutions. Moreover, the company’s commitment to excellence extends beyond mere provision, as it actively engages in collaborative ventures. The company’s globally unique application lab not only facilitates joint customer projects and scientific studies but also serves as a dynamic hub for hands-on demonstrations. This collaborative approach fosters a rich environment for learning and knowledge distribution, ensuring that the aerospace industry benefits not only from cutting-edge technology but also from shared insights and collective expertise.
In my opinion, the aerospace industry in India stands at the forefront of innovation and technological advancements, embracing additive manufacturing as a crucial element in its production chain. By leveraging cutting-edge measurement and inspection equipment throughout the entire manufacturing process, the industry can achieve immediate corrective actions, increase yield, and streamline resource utilization. With continued investments in high-quality metrology and research equipment, the aerospace sector can ensure the safety and quality of its intricate and complex components, further solidifying its position as a leader in technological innovation.
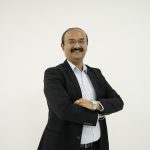
Delivery Sr. Director- Aero & Rail
Cyient