Bridging the gap: IPC-2591 CFX clears the way to the integrated smart factory
A major strategic issue occupies SMT manufacturers: Industry 4.0. Digital transformation, automation, integration of autonomous mobile robots (AMRs), connection to enterprise software – all of them are topics that are on everyone’s to-do list. At the same time, demanding and fast-growing markets for automotive and industrial applications require high levels of quality, flexibility and maximum transparency in the production processes. New products must be brought to market quickly and at competitive prices despite potential supply bottlenecks. The hardware and software landscape needed to churn out these products is diverse. Machines and systems usually come from different manufacturers and don’t speak the same language. With ASMPT’s Open Automation strategy and IPC-2591 CFX, the global standard for industrial communication, production and process data can be exchanged between machines, systems and companies in real time regardless of the equipment manufacturer. The seamless communication between all stakeholders involved in the manufacturing process makes production operations more efficient and effective and paves the way to the integrated smart factory.
Data is the driver for efficiency, quality and more added value in SMT production. Fortunately, data is readily available in modern SMT production. Systems and machine programs for material flow, setup verification and quality assurance paired with monitoring solutions as well as cameras and sensors in the machines deliver valuable information in abundance, with the only problem being that they don’t communicate on the same wavelength.
To optimally orchestrate people, machines, processes and material flows, ensure end-to-end M2M and M2H communication and be able to analyze and optimize processes across the board, you need to do more than collect, consolidate, evaluate and process data in isolated systems. Success with Industry 4.0 depends on open communication standards. They act as a link and ensure that the many bits and bytes from the systems and equipment made by different manufacturers communicate with each other so that processes can interact and employees be deployed efficiently.
With best-in-class hardware such as DEK solder paste printers, the Process Lens SPI system and SIPLACE placement machines in combination with the powerful smart shop floor management suite WORKS, ASMPT lays the foundation for productivity, flexibility and quality in SMT production. And with the modular, flexible and manufacturer-independent Open Automation concept, the global technology and market leader has opened another door to the integrated smart factory for its customers. For the seamless and secure exchange of data exchange between systems from different manufacturers, ASMPT relies on the open industry standard IPC-2591 CFX.

Global standard for industrial communication: IPC-2591 CFX
To seamlessly network machines, systems and companies in electronics production, you need communication standards whose parameters are accessible to everyone and whose use has been generally agreed upon by the industry all over the world. The global industry standard IPC-2591 CFX (Connected Factory Exchange) from IPC (the ‘Association Connecting Electronics Industries’, formerly called the Institute of Printed Circuits), facilitates machine-to-business and business-to-machine communication, thus laying the foundation for the electronics production of the future. IPC-2591 CFX enables the exchange of production and process data in real time and optimizes the recording of data as well as the traceability of products, with the latter becoming increasingly relevant for regulatory compliance and to meet customer requirements, especially in the automotive sector. The open standard published by the global electronics industry association IPC is based on a standardized command and data structure and can be deployed via plug-and-play. Suitable for the communication between machines and software as well as between applications, it covers all important areas: manufacturing, quality management, testing, ERP integration, and supply chains. It makes redundant and expensive in-house developments unnecessary, does not require IoT middleware, and supports important SMT instances such as MES, PLM, or ERP. It can also be read and interpreted by humans. By using AMQP 1.0 (Advanced Message Queuing Protocol), which was specially developed for the transfer of information between different systems and offers functions such as authentication, authorization, encryption and integrity protection, IPC-2591 CFX ensures highly secure and reliable data transmission.
Freedom with Open Automation
At ASMPT, IPC-2591 CFX has long been the de-facto standard for networking the company’s own product portfolio. In addition, ASMPT relies on the open standard for integrating third-party solutions and existing systems. To this end, the SMT specialist has developed with Open Automation its own strategic concept for financially feasible process improvements and targeted quality and efficiency gains. The forward-looking Open Automation approach gives electronics manufacturers complete freedom regarding the individual degree of automation and speed of implementation as they gradually retrofit and upgrade their operations on the road to the integrated smart factory.
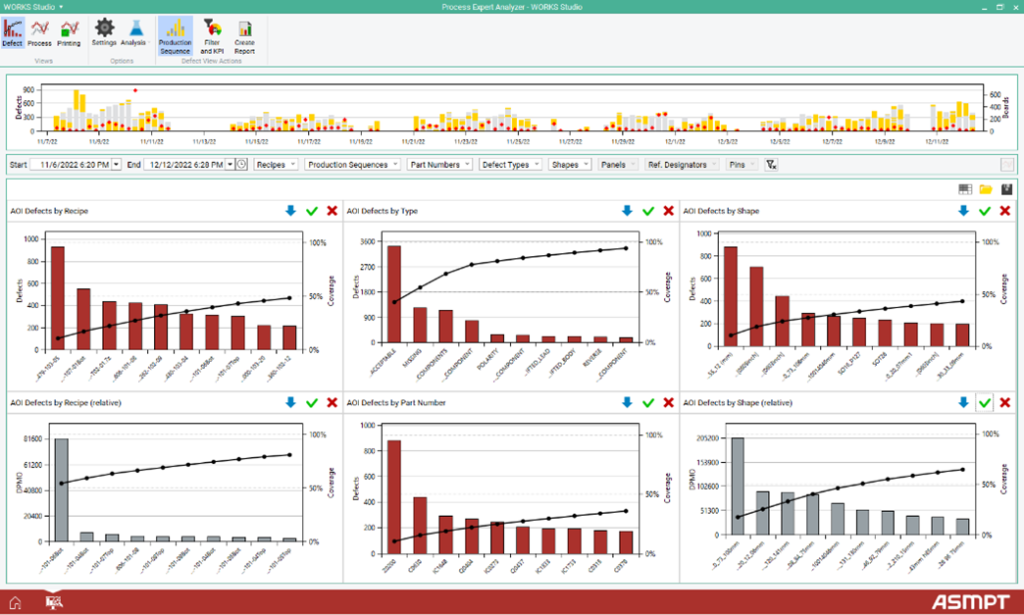
Improvements across the board
A prime example of the relevance of IPC-2591 CFX is the smart shop floor management suite WORKS from ASMPT with its WORKS Process Expert application, which optimizes SMT production lines that are equipped with DEK solder paste printers and SIPLACE placement machines. The application works in both the pre-placement and post-placement areas with solder paste inspection and/or automated optical inspection systems supplying automatically and continuously data that the software uses to further optimize the entire line. Using this information, DEK solder paste printers can even perform a fully automatic readjustment of the print offset or execute an understencil cleaning based on actual need.
In conjunction with SIPLACE placement machines, the application continuously evaluates the pickup data. If mis-picks of components accumulate, the software automatically generates a list of measures that an operator can carry out to fix the problem on the spot. Since the operator subsequently tells the application which of the proposed measures he or she has taken, the solution can use subsequent measurement data to determine which measures were successful. In addition, the real-time software uses big-data technologies to analyze all current and historical test data, which enables it to continuously improve.
Open to third-party inspection systems
Thanks to the IPC-2591 CFX standard, third-party SPI and AOI systems can be easily included in the optimizing feedback loop of the WORKS Process Expert application – a decisive factor for investment security. Examples include third-party AOI systems after the placement and soldering process. Such 3D inspection systems play an important role in quality control because they identify missing, misplaced or defective components, soldering errors or insufficient markings on the PCB and report such faults to the WORKS Process Expert application via the IPC-2591 CFX interface. “This compatibility based on the IPC-2591 CFX standard also applies to third-party SPI systems,” confirms Jerome Rousval, Solutions Marketing Manager at ASMPT, who nevertheless recommends his company’s own Process Lens 5D inline SPI system when purchasing a new one. According to Rousval, it was developed and optimized as a logical complement to the high-precision solder paste printers of the DEK platform. With its 2D/3D process, up to 20 million micromirrors and a measurement accuracy of up to 10 microns, the system delivers up to 70 percent shorter inspection times and up to 80 percent fewer pseudo-errors compared to conventional SPI systems.
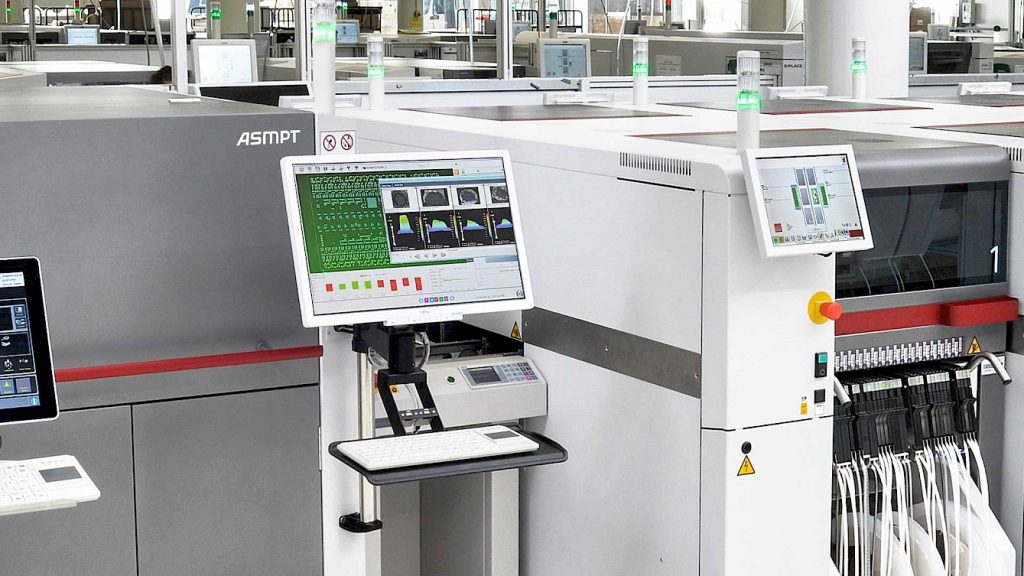
Compatible and future-proof
Regardless of which machines are being used, it quickly becomes clear that process-supporting and process-optimizing software and communication standards are prerequisites for the road to the integrated smart factory. Whether man, machine, or software – none of the actors involved in the production process should be regarded as an isolated system. Rather, SMT manufacturers are faced with the challenge of looking at their production as an integrated Industry 4.0 system, collecting holistic experience, and weighing up which solutions and processes they can keep and which they need to implement anew.
One thing remains, however: the data communication will continue to be based on the IPC-2591 CFX standard. It ensures that the integrated smart factory is always open for retrofits and that future investments will fit seamlessly into the current system. Or to express it in Rousval’s words: “Open standards are critically important, but equally important is the will of hardware and software manufacturers to apply them consistently so that customers will not be restricted by proprietary interfaces, which is what has prevented many SMT manufacturers from implementing useful automation strategies in the past.”
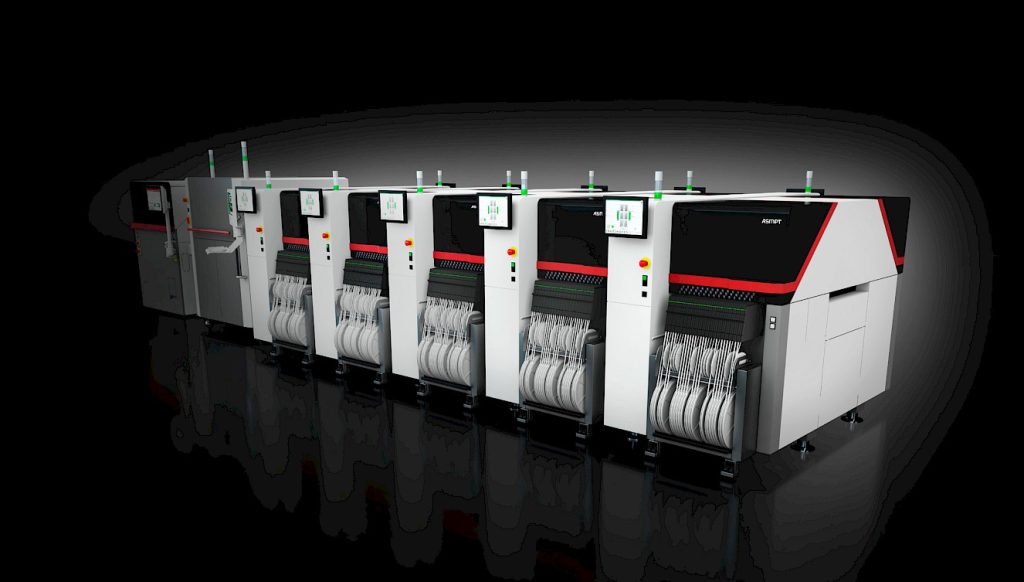