By Maurizio Di Paolo Emilio
Although cars have enjoyed a long and rich history dating back to the late 1800s, Electronic arrived relatively late to the party, only becoming an integral part of the automotive world in recent decades. Today, automotive companies fiercely compete not only with each other but also with the latest and greatest technology. However, it’s tough for CPU- and GPU-based electronic control units (ECUs) to keep up with consumer electronics, due to long chip-development cycles and the rigorous standards of reliability and quality applied to the automotive industry.
The automotive industry is using increasingly complex electronic systems to offer better security and efficiency to the driver. Field-programmable gate arrays (FPGAs) can play an important role in filling this gap by providing state-of-the-art performance and flexibility to system architects to customize their projects with a flexible (programmable) electronic circuit structure.
One goal in automotive design is to reduce the total number of ECUs, because they raise the total cost of the vehicle. Thanks to the latest FPGA advances, it’s now possible to combine electronic components within a vehicle more intelligently. For instance, implementing a purely CPU-based architecture is still a challenge. However, one possible solution being bandied about is a hybrid approach that combines CPUs and GPUs with an FPGA SoC.
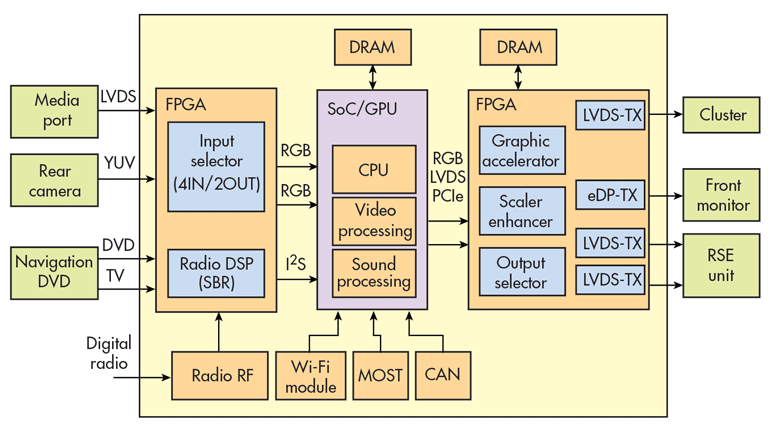
In the meantime, FPGAs are creating opportunities for automotive OEMs and suppliers to more efficiently build innovative safety applications, such as adaptive cruise control, driver assistance, collision avoidance, and blind-spot warning (Fig. 1). As the name suggests, driver assistance includes features such as reversing cameras, surround-view cameras, lane-departure warning systems, and pedestrian detection.
Hardware and Software
An FPGA is a semiconductor device based on a matrix of programmable logic blocks that are determined by the functionality. This feature distinguishes FPGAs from application-specific integrated circuits (ASICs) designed for specific design tasks. ASICs and FPGAs have several key benefits that must be carefully evaluated before deciding on one or the other. With the development of unparalleled logical density and a host of other features like digital-signal processing, clock speed, and a high-speed serial bus being available at lower prices, FPGAs become a solid proposition for almost any type of design.
Automotive infotainment systems, for example, carry great importance in modern vehicle design and significantly affect the sales of global vehicles. In these systems, it’s important to select the right main system processor to differentiate the user interface with the latest graphics. With multiple models to support, one may need to choose different systems-on-a-chip (SoCs) due to system variations and the emergence of interfacing technologies.
With an FPGA, the system becomes easily scalable, allowing the firmware to be upgraded remotely to support more manufacturers, regions, and models with minimal hardware modifications. Using FPGAs, any combination of I/O interfaces can be supported.
The most important electronic factor in FPGA design is that they’re considered programmable logic devices. The software of a CPU can of course be kept up-to-date, but the same can’t be said for the chip hardware of a computer. FPGAs, on the other hand, can be reconfigured or reprogrammed to perform different functions an infinite number of times. In many of the latest vehicles, the software monitors many functions during operation. Tesla’s S model already supports software updates via a 3G connection.
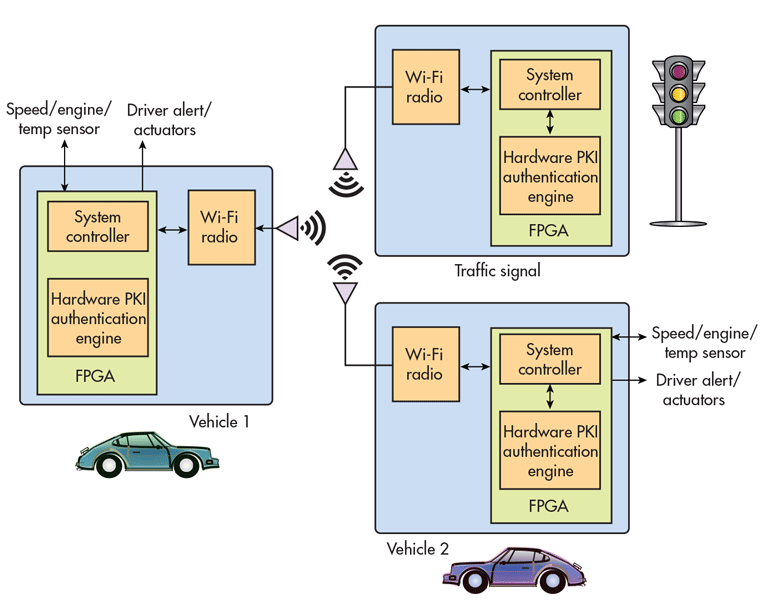
Thanks to this capability, FPGAs are able to keep OEMs up-to-date with the latest trends on programmable or configurable hardware architecture systems. So, when someone buys a new vehicle, electronically enabled functions may last longer because software and hardware upgrades can be made from your reseller or specialist store. Such software upgrades can be applied to different functions of the vehicle, which may incorporate more FPGAs as they become smaller and cheaper (Fig. 2).
Connected vehicles are able to analyze real-time information to provide new insights to vehicle users by optimizing their experience. Meanwhile, IoT connectivity can foster new business models for the automotive market, electronic market transforming the relationship between automakers and drivers.
The Automotive IoT
As automotive applications implement more IoT technologies, it becomes the nexus for innovations to converge—, particularly in the electronics industry. Yet, experienced engineers know there’s a learning curve when using something new, which comes in direct conflict with shorter development times. In turn, it escalates design risk.
For these reasons, designers tend to reuse the technology that’s already known, or they’ve used beforehand. Over time, this philosophy turns some architectures into widely used industry standards, while most others are used only in narrow market niches.
IoT engineers will have to resolve significant challenges such as electronic power-efficient and handling incompatible interfaces. An FPGA-based design approach can help to resolve these challenges, offering a fully functioning hardware platform for very-low-power IoT applications.
When investigating which 32-bit processor would better serve customer needs, many companies realize that a standard industry architecture offers significant advantages over a proprietary option. Standard industry processors generally come with a wide range of development tools, a significant volume of program code available, and a cadre of designers who have knowledge and experience in using them. Such benefits quicken project development time (and thus time-to-market) as well as reduce design risks, in turn giving customers a value-added solution.
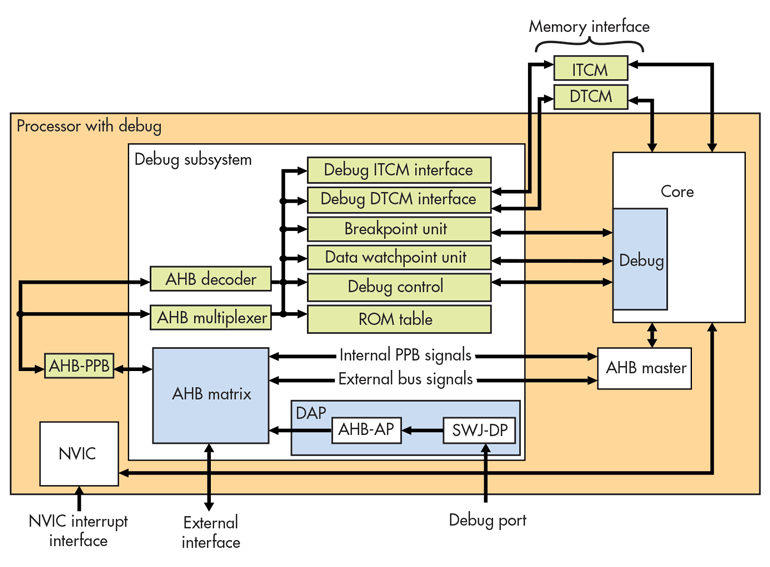
On this front, the ARM Cortex-M1 processor is designed from scratch for use in FPGAs. One fundamental feature it helps minimize the amount of resources needed to meet the application requirements. For example, debugging features (4 × breakpoint and 2 × watchpoints) can be included or removed; operating system extensions for system timers and software breaks are optional. The Cortex-M1 functions with most major FPGAs, which means migration from one FPGA device to another requires minimal effort (Fig. 3).
Summary
FPGAs are now implemented alone or together with CPUs in many automotive systems, as they provide more efficient and quick solutions for the hundreds of ECUs within a vehicle. They bring higher performance without consuming more power, and improve customization and scalability capabilities. FPGAs can help lower total car ownership costs, too, by integrating and reducing external components, accelerating time-to-market, and unifying the development flow.
Furthermore, by enabling innovative and cost-effective imaging solutions, FPGAs support the implementation of even more automotive functions. On top of that, they often offer a more cost-effective option in applications like motion- or motor-control systems. Going forward, expect the design needs of the growing hybrid- and electric-vehicle industry to drive the FPGA market as well.
Article Courtesy: www.electronicdesign.com