Reducing CO2 emissions in vehicles is a major challenge, and improving fuel efficiency is an important step in achieving this goal. To this end, 48V mild hybrid vehicles that provide good cost performance is expected to see increased adoption.
Growing demand for energy savings and the proliferation of mild hybrid vehicles.
A current social trend is the need to integrate countermeasures against global warming in all areas. The automotive field is no exception, establishing regulatory targets in each region for 2020, with the most severe restrictions enacted in Europe (95g/km). To achieve these limits many manufacturers are working on developing electric vehicles.
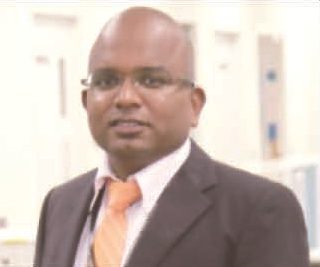
Design Center Head,
ROHM Semiconductor India
Makers of electric vehicles employ 5 main drive methods: Pure EV, powered solely by electricity, Fuel Cell EV that runs on fuel cells, Strong Hybrid, which charges using regenerative energy and supports electric-only operation, Plug-In Hybrids that can be charged with a standard AC outlet, and Mild Hybrid that charges a 48V li-ion battery using regenerative energy and adopts start-stop operation along with drive assistance. In the Mild Hybrid category alone, a total of 7.1 million vehicles are expected to be produced by 2024 (Fig. 1).
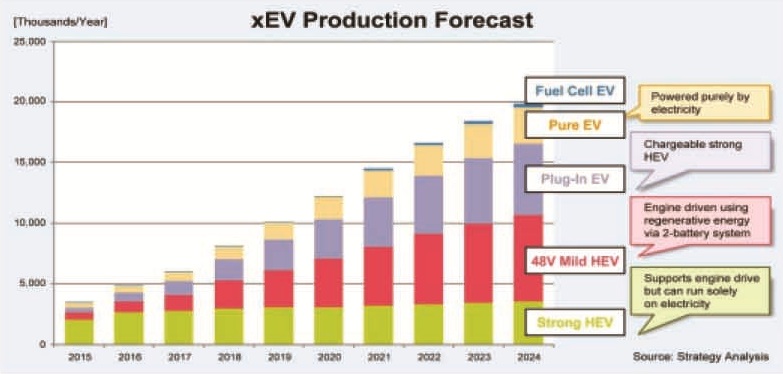
How does the shift towards electric motors improve fuel economy? In the case of conventional vehicles using gasoline-powered engines, a lead-acid battery charged by the engine powers all electrical systems, including lighting and AC. As a result, fuel efficiency decreases as the electrical systems are used, whereas in electric-powered vehicles regenerative energy (i.e. generated through braking) charges a lithium-ion battery that powers the electrical systems. This reduces the need to use engine power, improving fuel economy.
Strong Hybrid and Plug-In Hybrid systems are extremely effective in reducing CO2 emissions, but they entail significant additional costs and are difficult to install in compact vehicles. In contrast, 48V Mild Hybrid systems that provide a lower-cost solution while still reducing CO2 emission compared with conventional 12V vehicles are attracting increased attention.
Power supply ICs required for Mild Hybrid EVs
The major difference between Mild Hybrid and standard vehicles is the power supply voltage of the battery. Mild Hybrid systems utilize a 48V battery, quadruple the voltage of standard systems. However, because all other elements remain the same, including ECUs, the input /output voltage difference is significantly increased (Fig. 2).
Figure 2: Power Supply Differences
As a result, DC/DC converters with high step-down ratio capable of generating a low output voltage from a much higher input voltage is required. In addition, to prevent radio interference in vehicle-mounted power supply ICs, a switching frequency of 2MHz is needed to ensure that the AM radio band (0.5MHz to 1.7MHz) is not affected. Until now, 2 chips are necessary for stepping down the voltage from 48V to the 3.3V or 5V demanded by ECUs (48V→12V→3.3V/5V). However, this doubles the number of peripheral components, increasing mounting area significantly. There is also a way to use just one chip by lowering the frequency to convert voltage, but this method requires larger coils and capacitors that generate harmonics which can interfere with the AM radio band.
For these reasons, there is an increasing demand for DC/DC converters capable of directly stepping down 48V input to 3.3V or 5V output at a switching frequency higher than the AM radio band. But to achieve this a number of obstacles must first be overcome.
Monolthic Power Supply IC Utilizing Proprietary Nano Pulse Control Technology
One technical hurdle for achieving lower output voltage from a higher input voltage at high frequency is narrowing the switching pulse width. The switching pulse width of a DC/DC converter is a function of the input voltage, output voltage, and switching frequency, and is calculated by:
(ton: Switching Pulse Width, VOUT: Output Voltage, VIN: Input Voltage, f: Switching Frequency)
As can be seen from the above equation, the switching pulse width narrows as the input voltage increases, output voltage decreases, and frequency rises. Therefore, a method for reducing the switching pulse width is required for 48V Mild Hybrid systems. But to reduce pulse width it is first necessary to solve problems related to noise generation during switching.
Increasing the input voltage will cause the noise component to increase during switching due to parasitic inductance contained in the IC. The noise component will also rise at high frequencies, resulting from the increased switching frequency and parasitic capacitance of the element (Fig. 3).
Figure 3: Noise Component Increases at Higher Voltages and Frequencies
When this switching noise is introduced into the IC unstable operation may occur. To prevent this, conventional control methods utilize mask time. Also, an analog circuit is required for operation, introducing a delay time. These two factors that arise due to the increased noise component cause the pulse width to become wider.
In response, ROHM developed a new technology, Nano Pulse Control, which leverages high voltage BiCDMOS processes and ultra-fast pulse control circuitry to detect information before noise is generated and perform appropriate control.
The BD9V100MUF-C is the first IC released using this technology. The pulse width required to 3.3V output from 60V (the maximum voltage required for 48V power supplies) is 30ns, but when considering load and power supply fluctuations within the IC a narrower pulse width is needed. ROHM’s IC is capable of high-speed 9ns pulse control, much shorter than 30ns, resulting in the industry’s highest step-down ratio of 24:1 and enabling 2.5V output from 60V input (a pulse width of 20ns is required to step down 60V to 2.5V.) (Fig. 4) This high-speed control makes it possible to provide stable 2.5V output from an input voltage range of 16V to 60V at a high frequency of 2MHz or more (Fig. 5).
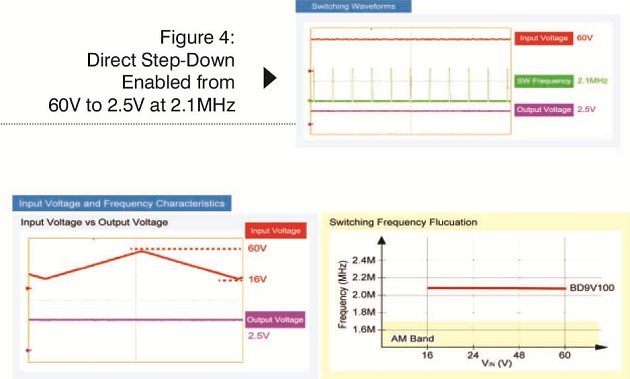
Utilizing ROHM’s IC allows users to configure DC/DC converters capable of stepping down 48V to 3.3V with a single chip, instead of conventional systems that require 2 chips to first convert 48V to an intermediate voltage such as 12V, then from 12V to 3.3V.
Our approach for the automotive market includes developing these automotive-grade ICs that integrate protection functions to prevent IC destruction even during abnormalities. When the input voltage increases to 60V and the output and switching terminals are shorted a large amount of energy is generated, causing large current flow which can lead to destruction in ICs employing conventional short-circuit detection methods. In response, we developed a new type of protection technology that detects abnormalities beforehand to protect the IC against large currents. Also, adopting a wettable flank package that provides superior wettability and visibility contributes to improved mounting reliability.
Support for the industrial equipment market
Besides the automotive sector, 48V lithium ion batteries are expanding to industrial applications such as base stations and construction equipment. Many MCUs used in these sets operate at 3.3V or 5V (as in vehicle systems), enabling compatibility with ROHM’s Nano Pulse ICs. And high frequency operation that cannot be achieved with existing solutions will make it possible to reduce peripheral component size.