Launching a spacecraft or satellite is incredibly expensive, with no possibility of recovery or repair. Therefore, you must have a test solution that can verify the spacecraft’s power management system on the ground before launch.
These test systems must be capable of accurately simulating the conditions faced in space. These systems must emulate the effects of varying operating conditions, including changes in light intensity, temperature, and shadow. The power testing instruments must be able to do this at multiple operating conditions and achieve consistent results.
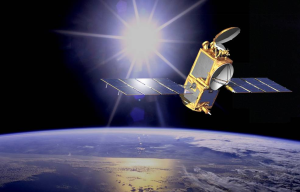
The good news is that there is dedicated test equipment with these capabilities – purpose-built solar array simulators (SAS). In contrast to custom-built solutions, commercial SAS solutions offer the following advantages:
- Predictable delivery
- Enhanced reliability
- Published, verifiable specifications
- Easier calibration, maintenance, and repair
Problems with using a general-purpose programmable power supply
You may consider using a standard programmable power supply to test a satellite’s power system, but there are three key reasons why this is not a good solution.
Output Capacitance
General-purpose power supplies are designed to provide stable voltage levels under changing load conditions. These power supplies are not good SAS solutions because solar panels are current sources. A good SAS solution must be designed to function as a current source.
Solar output flexibility
Conventional power supplies have a rectangular operating locus and adjust voltage and current along this “curve.” In contrast, solar array panels have exponential shaped IV curves, and a SAS must be able to rapidly shift along a given curve or quickly transition to a different curve. This capability allows the SAS to accurately emulate changing irradiation levels and temperatures or the effects of spin, eclipse, and shadow.
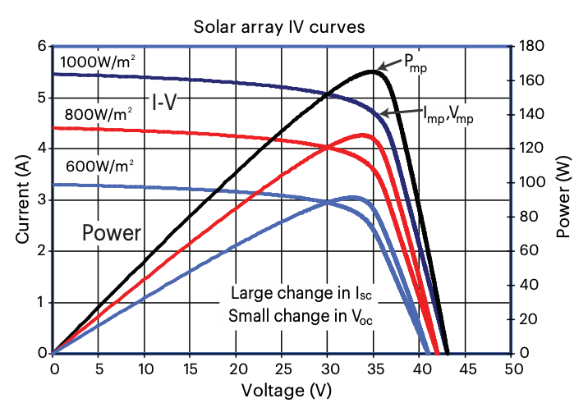
DUT Protection
Due to the fragile nature of satellites, conventional power supplies cannot meet the protection levels required to keep satellites from being damaged. Conventional power supplies do have built-in overvoltage protection and overcurrent protection. These basic capabilities, unfortunately, are insufficient to limit transient current spikes or protect internal components against power dissipation.
Additional Requirements for an Optimal SAS Solution
In addition to the key requirements mentioned above, an optimal SAS solution must offer the following:
A wide array of output ratings
Critical specifications for a SAS solution include current, voltage, power, and shunt-switching speed. The wider the variety of choices, the easier it is to select the best combination of power levels and shunt speeds to meet the requirements of a specific satellite design.
Size and power density
Satellite arrays can be comprised of 48 PV segments or more. Therefore, SAS test equipment must have numerous outputs. This can result in SAS test systems filling up many slots in a test rack. Thus, power density is critical, especially when space is at a premium in a rack system.
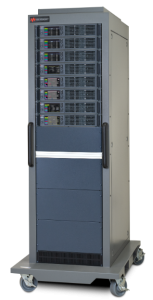
System-level considerations
A SAS is generally a component in a larger rack-based system. This makes configurability and serviceability critical considerations.
It is crucial to consider the ease of configuration for initial use. In a single-purpose system, modularity enables reuse in future systems. For multipurpose systems, dynamic reconfiguration helps ensure faster changeover. In either situation, interconnect features such as barrier-block coupled with relays simplify reconfiguration.
It should only take minutes to service instruments to limit downtime rather than hours or days. A modular SAS can help achieve this by allowing you to remove and replace individual power modules quickly. The barrier-block / relay interconnect scheme mentioned above simplifies self-test procedures by supporting rapid disconnection and reconnection.
Authored Article by: Brian Whitaker, Keysight Technologies