PHILIP LING | Avnet
Factory automation strategies are reaping benefits now from several technologies and their enabling elements.
Automation has a long history, and it has played an essential role in all industrial markets. Repeatable manufacturing to high quality and in high volume is the essence of industrialization. The cost of the finished product can be directly related to the level of automation in the manufacturing process.
Continuous advancements in automation deliver mechanical excellence. That excellence, in turn, relies on control. Manufacturers must balance technologies used to implement control to this level with commercial considerations. These include the cost of development and deployment – or capital expenditure – and the recurring cost of implementation – or operational expenditure.
New technologies can impact factory automation when manufacturers align capex and opex while accurately assessing total cost of ownership. This article examines some technologies that meet this requirement and some that may influence the direction of automation.
Industrial automation technologies
Several technologies with their corresponding enabling elements are impacting industrial automation right now. The competitive advantage of Industrial Internet of Things (IIoT) will increase as these technologies become more pervasive.
- Single-pair Ethernet
- Edge computing
- Time-sensitive networking
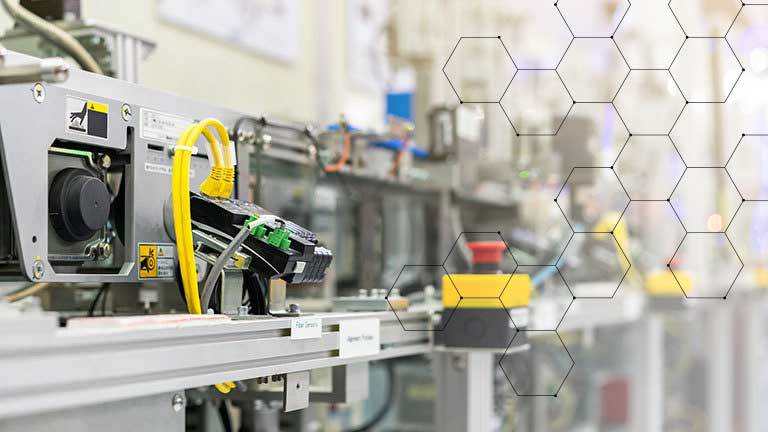
Single-pair Ethernet in industrial automation
Wide area networking (WAN) has changed every aspect of modern life. Consumers enjoy internet access anywhere, even on a transatlantic flight. Its use in IIoT means information technology and operational technology are colliding, and the way connectivity is used is still developing. Different parts of the ecosystem are at different stages of their IIoT journey.
The industrial sector is now largely aligned on the use of Ethernet to support an IP architecture. There is also growing momentum behind single-pair Ethernet (IEEE 802.3cg) in industrial automation. The move to single-pair Ethernet (SPE), which the automotive market developed, provides a simplified network at the physical level. It offers both data and power on the same two wires, speeds of 10 Mbps, reaches of 1000 meters, and support for multidrop configuration.
The development of SPE is helping to bring Ethernet into an environment where single-pair connectivity has long been the preferred solution. SPE’s significance will increase as support grows. An example of this is the advanced physical layer (APL) developed by leaders in the industrial sector. Ethernet-APL uses the 10BASE-T1L part of the standard, plus extensions. Ethernet-APL covers physical layer attributes, including power, connectors and cables. The Ethernet-APL layer is also specified for use in hazardous areas.
The Ethernet-APL group comprises OPC Foundation, Profibus, FieldComm Group, and OVDA. The physical layer supports various high-level network protocols, including EtherNet/IP, HART-IP, OPC UA, and Profinet.
Edge computing
The IIoT introduced cloud computing to the factory floor. Cloud platforms play an important role in data aggregation, its analysis and distribution to back-office applications. Edge computing puts the power of the cloud directly on the production line.
An edge computing solution employs high-end processors running cloud-level software on a local device. That device connects directly to the manufacturing equipment. There are several reasons why edge computing is popular.
First, it allows some of, or all, the operational data to stay inside the organization’s walls. There are good security imperatives for taking this approach. A further reason is to simply minimize the cost of moving data around. Another is to avoid the latency associated with processing time-sensitive data in a cloud platform.
Second, edge computing creates a contained environment that enables manufacturers to take greater control over their processes. This work cell approach can support distributed and separate workflows that provide greater flexibility over how assets are deployed. An edge computer can turn a small cluster of machines into a discrete manufacturing process that can operate outside a wider manufacturing environment.
The concept of edge computing goes beyond securing data or minimizing cloud transfers. It supports trends such as micromanufacturing or on-demand manufacturing.
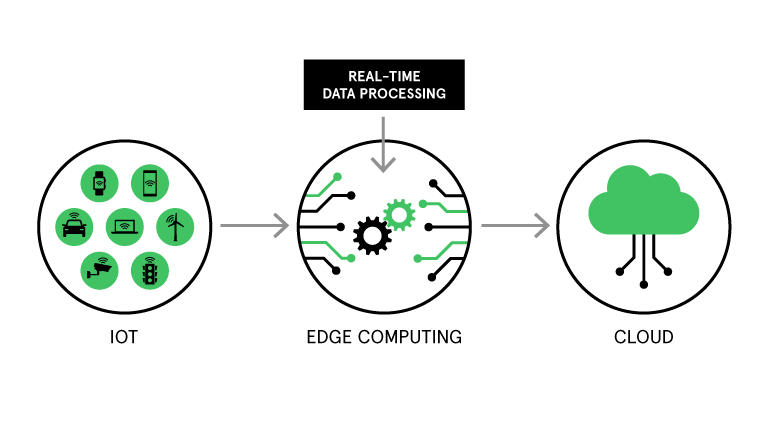
Edge computing in industrial automation
Time-sensitive networking
As the IT and OT networks continue to merge, the need for time-sensitive networking (TSN) has increased. The IEEE Standards Association is working on several profiles for time-sensitive networking in various verticals, including industrial automation.
The purpose of the specification is to support time-critical packets on an Ethernet network. It achieves this using three mechanisms. The first is a method to prioritize Ethernet frames that are time critical by delaying frames that are not. Transmission time is one tool used to set priorities. It also looks at the frame length to determine if it can be sent without disrupting higher priority traffic. A further method is to build fault-tolerant networks with multiple paths to avoid latency.
Semiconductor manufacturers are now implementing these features at the chip level. Multi-chip solutions are evolving into single-chip or system-on-chip product offerings. This will continue in parallel with efforts to move to standard application protocols.
Expect the cost and complexity of implementing TSN to come down quite rapidly. Not all manufacturers will see a benefit or need for TSN, at least not immediately. As IIoT pervades the manufacturing environment, TSN is likely to feature more strongly.
Technologies that will impact factory automation
Industrial equipment has a long operational lifetime. This means change can be slow in comparison to other markets. As an example, wireless mesh networks are still mostly limited to connecting sensors in an industrial environment. Wired connectivity is still dominant for control.
However, there is also more cross-pollination between verticals, encouraged by wide area networking. Many of the technologies that have been created in – or are dependent on – IT are making their way into the OT world. Some of the prominent and most promising technologies include:
- Digital twins
- Blockchain
- Microservices
Digital twins
The idea of operating duplicate systems, or twins, in different environments goes back to NASA’s early days. A twin can be used to replicate and react to operational data happening somewhere else, even off planet. Moving to the digital domain has enabled the concept to be more cost efficient and, potentially, more flexible.
Digital twinning involves modelling an action, rather than simulating it. The difference relies on the twin using real-world data. This is where IoT technologies play a part. Sensors are the primary source of data.
Digital twins in industrial automation
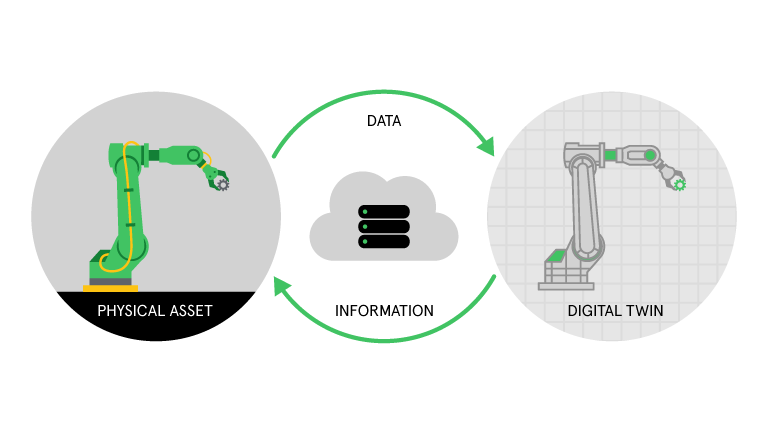
It becomes feasible to use digital twins as manufacturers deploy more sensors on industrial equipment and couple them with high-speed networking.
Recent developments indicate OEMs are now implementing digital twins at a work cell level. This makes it easier to model part of a system as a function, rather than trying to model an entire factory.
Using multiple digital twins will become more common with the development of edge processing. It follows that the two are closely coupled, as edge processing is effective at a local level. Although edge processing is not dependent on digital twinning, the symbiosis is apparent.
Blockchain
In a manufacturing environment, the term “blockchain” can be closely associated with supply chain. Engineers have discussed the concept of using blockchain technology to authenticate and track the products in the supply chain for several years.
Part of the potential in adopting IoT comes from the commercialization of information. Trust will be an important part of the success. Using blockchain to provide evidence of authenticity could be key.
The move toward providing something as a service is also building momentum. Here, blockchain could be used to validate the hardware platform delivering that service. If the service relies on genuine parts being fitted to a system, blockchain could be the best way of authenticating those parts.
Microservices
If a theme is emerging in industrial automation’s evolution, perhaps it’s around making work cells more intelligent. Edge computing and soon digital twins are focused on work cells and modular functionality.
Modularity at a software level is one way to describe microservices. The methodology is now common in cloud platforms. A microservice architecture is more agile, more scalable and easier to maintain than large monolithic software structures.
The diversity in industrial automation processes suggests microservices will become more common here, too. Flexibility on the shop floor will mean machines can be repurposed more frequently. Using a microservice approach will support that flexibility.
AI in industrial automation
There is enormous scope for AI to impact industrial automation. Current examples of AI demonstrate that the technology is good at following procedures and adapting within known parameters. Its real strength comes from reacting to the unexpected in a predictable way.
Using AI in this way should improve procedural operations that are handled by programmable logic controllers (PLCs). AI can also now write the ladder logic that configures the PLCs. This scenario uses AI in a mechanical way to augment a function.
Putting AI into human-centric operations may be the next phase. In this scenario, the AI would need to “think” like an operator. It would at first assist and, potentially, in time displace the human in the loop.
Conclusion
Industrial automation is constantly developing. New technologies, often from other market verticals, provide the momentum for improvement. Caution is always used, but the pace of change seems to be increasing.
Studies show a widening productivity gap between large OEMs that can afford to implement new technologies more aggressively than smaller enterprises. As access to these technologies improves and the total cost of ownership softens, this gap may once again close.