The sudden outbreak of COVID-19 has left no hope for industries and made so many of them stranded on a sinking ship. The present conditions are very much fragile and every sector of Indian industry, be it manufacturing or distribution, hospitality or tourism, automobile or aviation are the prime sufferers. Every niche of the industry is facing a lot of difficulty and hoping to see a change one day or the other.
The Electronic Industry is no good, the reliability of Indian Market on imports has very much affected this time of the year as the operations and logistics dealing with foreign imports is at halt thereby making the industry void. The self-proclaimed intrinsic unit of the industry tooling i.e. the component industry is one such affected industry. Components are the basic element required for manufacturing and then later for commercial purpose. COVID-19 has also left lot of repercussions on the component traders, manufacturers as well as distributors.
ELE Times got the opportunity to have a brief talk with some of the industrial players in component market. Let’s have a look at the perception of the industry from its good and consistent professionals.
Element 14
“There will be need to become much intense search for alternative suppliers from countries with competitive products”
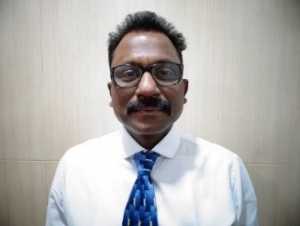
Speaking with ELE Times on the impact of coronavirus, Anil Kumar Challyil, GTC Site Manager, Global Technical Marketing, element14 comments that the coronavirus (COVID-19) continues to have an unprecedented impact on everyone’s lives and it will undoubtedly continue to impact global demand for components. Manufacturing was heavily impacted in April, May, and June primarily due to the closure of factories during the lockdowns. Even in those areas where factories could have functioned, there was no way for components to reach factories or finished goods to leave factories. Financial pressure and uncertainty also impacted the overall demand, which unsurprisingly dropped during the period. Manufacturing has recovered in July, but the company expects it will take longer for the market to fully recover. Design decisions, new product launches, and time-to-market are all being delayed, creating a long term impact on the industry.
There is a conscious effort to retain the workforce, and make fundamental changes to supply chains to improve resilience. Key changes will support a return to a more normal operating environment and going forward, we expect that local-to-local supply chains will be needed to provide more flexibility. In addition, companies are increasingly adopting e-commerce and digital analytical tools to match supply and demand.
He further mentioned about the severe impact of importing everything from different countries and thinks that being a sole reliant on one country as the supplier of products and components is never a good idea, everybody knows this, and discussions of reducing dependency on China had existed much before COVID-19 times. However, electronics product suppliers and manufacturers preferred to maintain status-quo, considering the substantial economic advantage provided by China.
As we enter this new world, there will be need to become much intense search for alternative suppliers from countries with competitive products. Manufacturers are facing severe cash and capital constraints because of the pandemic, and will, therefore, be very cautious before making quick moves. In short, the dependency on supply chains from China will continue as relocating entire supply chains is easier said than done. The huge captive consumption market could encourage domestic manufacturers with existing facilities to increase their production facilities and become more competitive. This needs creation of a best in class manufacturing ecosystem that offers efficient and highly trained manpower, encourages innovation, allows ease of doing businesses and protects intellectual property.
The company solely believes in an optimistic approach and claims that the commercial market is exceptionally price-conscious, it won’t be easy to move to a position where it doesn’t rely on China at all. Eventually, economic viability will once again become the primary factor in making buying decisions. China is India’s largest trading partner for electronic products and industries such as consumer electronics could become
paralyzed without the import of crucial components and subsystems from China. Indigenously manufactured components or products have to be competitive to succeed. Indian manufacturers can lower their costs by addressing more significant market volumes, and there is a large captive domestic market available to them. India should focus on the key, high volume components, such as discrete and analog semiconductors, passive components, and displays that require lower investments on IP and manufacturing. If local manufacturers are offered incentives, and entry barriers are created for the imported parts, the Indian electronic component industry can hope to do reasonably well.
China will continue to remain the dominant supplier, but surely, there will be a substantial increase in the electronic manufacturing business in COVID-19 India and China’s share is expected to go down as other supply chains, including domestic component manufacturers, emerge. The dominance of e-commerce is already on the rise and will establish as the primary channel of sales and customer reach. Distributors with a good digital presence, advanced level of technical support, design content will become quite valuable. In all challenges there is opportunity, and both the govt. and the private companies are reacting to it. A new incentive program called the “Production Linked Incentive Scheme (PLI) for Large Scale Electronics Manufacturing” Is targeting makers of mobile phones and specific electronic components by offering them financial incentives to start or build up their existing domestic manufacturing capacity. Major mobile phone brands and telecom operators have made significant investment announcements recently. Defense, Power infrastructure, Medical, will be focus segments as there is an immediate need for self-reliance.
Singodia Electronics Pvt. Ltd.
“Majority of the customers are still willing to switch to Non-Chinese suppliers despite of not being price competitive to Chinese suppliers…”
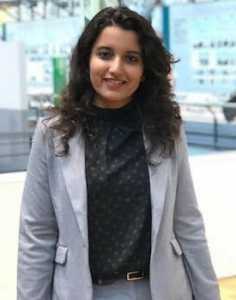
Interacting with ELE Times on the repercussions faced by the component industry, Parul Saini, Business Development and Sourcing Head, Singodia Electronics says that the lockdown due to COVID-19 has stopped all the business activities in India as well as internationally. The company started to face issues even before the lockdown was imposed in India as lockdown imposed in other countries like China, Singapore, South Korea stopped all the international shipments to India. The entire supply chain was disrupted for almost 3 to 4 months. Many of the air shipments too were on hold but sea shipments were still in operation. Proper tracking of all shipments with freight & forwarders were followed up constantly to release shipments whenever government offered lockdown relaxations. Limited employee capacity and rising containment zones led to increase in freight costs as many migrant workers shifted back to their native place and there was shortage of manpower. In addition, Air and sea freight charges increased exceptionally. Industries had to bear heavy freight charges and long lead times to keep running businesses during this pandemic. However, frequent lockdown relaxations have brought some relief to many businesses and the industry is getting back to normal.
Further mentioning about the impact of importing from china and the need to change this, she further added an optimistic approach by mentioning that COVID era was an eye opener for all Indian manufacturers and distributors as everybody paid less heed to ‘Made in India’ products and focused on imports considering better pricing and faster delivery.  It was realized that it is the time to be more vocal for local to boost domestic manufacturing, while this is harsh truth that China is the major supplier of electronic components in India and the sector is heavily dependent on China. Considering current political sentiment against China, India still can’t do without China offering competitive pricing and availability. However, Chinese attitude has changed the mindset and many Indian manufacturers are fine with shifting to suppliers other than China. Keeping track of all this statistics, Singodia Electronics conducted a small survey with their regular customers to understand the current electronic components market where more than 70 customers participated across many industries such as LED Lighting, Energy Meter, UPS/Inverter, Consumer Electronics and Industrial Electronics.
Key Takeaways:
- Majority of the customers are willing to switch to Non-Chinese suppliers.
- Majority of the customers are still willing to switch to Non-Chinese suppliers despite of not being price competitive to Chinese suppliers, and demand good quality.
- Many customers are considering Indigenous Component Manufacturers offering competitive pricing and quality products.
- Some have stopped considering COO (Country of Origin) China for existing and new projects
- Some have already switched to Non-Chinese suppliers
- More than 60% of customer’s current BOM (Bill of Material) of electronic components covers Chinese suppliers.
Parul further added that Indian component manufacturers provide much better-quality components but are not sometimes price competitive as compared to Chinese suppliers. In reference to the above mentioned survey, 90% of the customers are still willing to switch to less price competitive Non-Chinese suppliers, creating a huge opportunity for Indian component manufacturers. They prefer to procure from indigenous manufacturers because of immediate availability and transactions in Rupee. Many manufacturers also want to avoid the complication of import process such as currency fluctuations, freight and Forwarder cost, custom duty clearance, import duty etc.
The Coronavirus crisis made us realize the need for becoming Atmanirbhar. This is a good wake up call for all manufacturers from different industries towards becoming self-reliant and promoting domestic manufacturing. There are good opportunities in local manufacturing of electronic components such as MLCC, Chip resistance, Crystals, relays, ICs, Transistors, LED chips etc and invest in technology and machinery to enhance Indian components market. Indian components and trading business will have to upgrade the knowledge and technology as per the industry demand. There is a huge scope in the electronics industry in various sectors such as Medical Devices, IOT, Solar Products, Electric Vehicles, Drones, etc. The road ahead will foresee more Indian component manufacturers in product portfolio than currently and will try to replace Chinese suppliers in the long run towards efficient and consistent trade.
For more information, visit element14.com  and singodia.com
By Mannu Mathew | Sub Editor | ELE Times