When we think of space exploration, the focus often gravitates toward massive rockets, sophisticated spacecrafts, and the captivating images they send back to Earth. However, the unsung heroes in these endeavors are the critical components ensuring that every part of these complex systems communicates effectively. One of the most critical components enabling this communication is connectors.
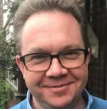
From the Artemis program’s monumental lunar missions to the revolutionary insights of the James Webb Space Telescope, the success of these missions hinges not just on the large-scale engineering feats but also on the reliability and performance of connectors. These ubiquitous components face the extreme conditions of space and are pivotal in every step, from the rigors of launch to the harsh environment of outer space.
Space Exploration Ascending
Space exploration, both by government organizations and commercial ventures, is very much in the news. One of the most extensive programs in recent space history is the Artemis program, which will see humans return to the Moon. The Space Launch System (SLS) completed its first successful test mission in December of 2022 and forms the largest component of the program. However, the latest steps in our return to the Moon are not the only exciting initiatives in space.
While these high-profile events capture the public’s imagination, they represent just a small part of the picture. Exploration and exploitation of space are everyday activities. More than 200 space launches were made in 2023 alone, carrying science missions and satellites into orbit and beyond.
The Extreme Conditions of Space
Even though spaceflight has become more common, the conditions in which these systems must perform are unlike any other. Space represents possibly the single most demanding environment known to engineering. Any equipment used in spaceflight is exposed to a range of extremes, from high and low temperatures and harsh radiation to the severities of the launch process and the vacuum of space.
The lack of atmosphere in space is incredibly unforgiving. On Earth, our atmosphere is a protective blanket that provides pressure, thermal insulation, and safety from harmful radiation. This protection is stripped away in space, exposing equipment to potential damage.
Without the atmosphere to protect it, an object in space receives the full force of the sun’s radiation. When equipment is bombarded by direct sunlight, its temperature can quickly become dangerously high. In contrast, the parts of a spacecraft that remain in shadow are very cold. These temperature extremes, must be considered when selecting the materials to use aboard space vehicles. Other radiation sources, including galactic cosmic rays, are highly ionizing and can harm delicate instruments or sophisticated electronic circuits.
Choosing the Right Materials for Spaceflight
The lack of atmospheric pressure also causes materials to behave in unique ways. Components employed for spaceflight can face an array of challenges that affect performance. Outgassing is when a gas trapped inside another material is released. This is a common problem when plastic is exposed to a vacuum during spaceflight, but it is not limited to plastics alone. Some metals, including zinc and cadmium, are also prone to sublimation in vacuum conditions, both of which are commonly used in conventional equipment design.
In both cases, the gas that is released can cause damage. It may condense onto cold surfaces such as the optics and sensors of scientific equipment, which can degrade or even negate their effectiveness and put the entire mission at risk. NASA and the European Space Agency (ESA) have recommended volume levels of outgassing for materials used in their space applications. These recommendations play a key role in selecting components for spaceflight.
Components also need to be mechanically robust, as launching satellites, probes, and spacecrafts into orbit exposes them to acceleration and vibration that can cause damage that might be undiscovered for months or years. As such, plastic components need to be manufactured using materials that exhibit high stability, even in vacuum conditions.
To provide solutions for these demanding conditions, connectors designed for spaceflight must be amongst the most advanced in the industry. Manufactured to stringent standards and tested to prove their performance even in the vacuum of space, they are the very definition of high-reliability connectors.
Engineered for Maximum Endurance
If the spaceflight environment is not challenging enough, there is one additional aspect that contributes to the difficulties of designing for spaceflight: endurance. Whether intended for commercial or scientific purposes, space missions can last for years. If a piece of equipment fails, gaining access to fix the problem is essentially impossible. In these circumstances, designers and engineers depend on the reliability of each component that makes up the equipment, no matter how small.
Endurance also plays a crucial role in power planning. A long-range probe operates on a stringent power budget, and any component that introduces unwanted electrical resistance will risk jeopardizing the mission. The electrical terminals of connectors designed for space applications are made from high-performance materials and coated with a thick layer of gold, ensuring minimal electrical resistance to reduce power loss.
Contacts with low electrical resistance provide additional benefits beyond power planning. The instruments on space probes take highly precise measurements, and the currents generated by these sensors can be extremely small. For these tiny currents, low contact resistance is crucial to maximize the likelihood of detecting critical signals.
With endurance in mind, connectors designed for spaceflight applications use materials that provide the best possible performance by reducing interference. Manufacturers must ensure that the magnetic signature of any component is minimized to prevent interference with precision scientific experiments. The connector shell also protects against electromagnetic interference (EMI). Vehicles that must traverse the vacuum of space are unprotected against solar radiation, which can interfere with scientific observations and damage sensitive instruments. This is another reason why the shells of spaceflight connectors are gold-plated, which provides the highest possible protection against EMI in these circumstances.
Mission-Critical Connector Engineering
Connectors play an often-overlooked role in spaceflight applications. Space vehicles are typically manufactured from sub-assemblies, which are brought together before launch. Connectors provide the vital interface between each system during the extensive testing regime before launch and the demanding conditions in space. Spaceflight connectors are designed according to some of the highest standards in the interconnection industry and, as a result, represent some of the most capable products available today.
By David Pike