Among all of the buzzwords to describe the increased electrification of our world, one term should stand out more: current sensing. Few of the innovations you hear about in solar power arrays, electric vehicle (EV) charging stations or robotics would be possible if current-sensing technology wasn’t reliable, accurate and easy to design with.
In this article, I’ll address four key design trends that have emerged from the growth of electrified applications and the current-sensing technologies intended to address them: higher system voltages, increased system protection, telemetry monitoring and reduced form factors. Overall, current sensors are monitoring a vital parameter, current, in an electrical system and this allows for a system to operate as efficiency as possible in a safe range.
Support for higher system voltages through current sensing
As efficiency requirements continue to become more stringent system voltages are increasing as a result to help drive efficiencies. With higher system voltages the amount of current that is delivered to a load can be decreased to create an equivalent amount of power, based on Ohm’s Law, which helps reduce I2R losses in a system. Higher voltages make it more efficient to pass large amounts of power across a system because the current range is lower, generating less heat in stages such as AC/DC or DC/DC power inverters.
The EV charger shown in Figure 1 is routing power off the grid, which could be at voltage levels such as 120 VAC, 240 VAC, 230 VAC (one phase) or 400 VAC (three phase). The typical EV charger routes AC power from a grid to an EV onboard charger, which converts the power to DC and delivers charge to the batteries.
In a DC fast charger, AC power goes into the EV charger from a grid, is converted from AC to DC within the charger, and delivers voltages as high as 920 VDC to the batteries for faster charging. Stepping up to higher voltage levels and keeping similar current levels makes it possible for more power to pass directly into the batteries, making for quicker and more efficient charging.
Current sensors help increase system efficiency in EV chargers in and can be used in multiple locations throughout the system. These sensors can be used in the AC line inputs, which monitor current in order to adjust reactive power into the system on the front end. Another is after the power factor control loop and secondary DC/DC, either on the positive or negative node of the system; this configuration monitors for faults.
There is also a location between the primary DC/DC and secondary DC/DC, where current sensing from differential amplifiers be used for flux balancing. In addition, it’s essential to use isolated current sensors like the AMCS1100 or TMCS1100 to protect the system and humans interacting with EV chargers
Increased system protection
Electrification also increases the need for system protection which ensures that a system reacts promptly to an event outside the safe operating area to avoid damage to the semiconductor and other sensitive content. In most systems, some form of system protection ensures that the system operates as intended. For example, if the robots shown in Figure 2 pick up an unusually heavy item, there may be a significant current spike in the motors.
Figure 2: Industrial robots
A current spike may indicate that a load is beyond the robot’s capability, which could potentially damage the content in the system or the physical robotic arm. A current-sensing device with an integrated comparator would see the peak current, perhaps beyond the safe operating area of the system, rush into the electric motors. The INA301 with integrated overcurrent comparator could react as quickly as <1 µS and set an alert, which may cause the system to shut down. This is similar to a point-of-load measurement, where shunt-based sensors like the INA228 and INA226 ultra-precise bidirectional current sense amplifiers can monitor current flow and voltage-levels through a particular node to ensure that the node remains in its safe operating area.
Enabling telemetry monitoring
As applications become more electrified, the requirements for monitoring increase to track both consumption for energy ratings and better predictive maintenance events.
An example of monitoring or telemetry monitoring for predictive maintenance is by data logging the current and voltage levels going through the cooling fans in rack server systems. Using a device such as the INA232 will data log the fan’s power consumption. Data logging enables the system to alert technicians that the fans may be acting erratically or nearing the end of its life.
Leveraging a digital power monitor is an appropriate style of device for this use-case, since it takes in both bus voltage and current flow information. Digital power monitor ICs do arithmetic onboard to calculate power, charge and energy and transmits this information (plus the bus voltage and current-flow data) through I2C or serial peripheral interface. Doing the arithmetic on-chip offloads processes from the CPU or microcontroller, so processing resources can be used to handle other tasks more effectively. This is especially important in systems, where the CPU or microprocessor are handled many tasks.
Reduced form factors
As more applications include more electronic components or are needing to fit in smaller spaces, there is a greater need to reduce the size of the components or increase the number of features per unit to help reduce overall board area. Many systems, such as smartphones and robotics systems, are size-constrained and require a constant reduction in size and increased feature sets.
Smaller current-sensing devices allow designers to increase the amount of monitoring throughout or to reduce the system’s overall size. Both cases could be advantageous depending on the overall system parameters – reducing the size of integrated circuits (ICs) or increasing the number of features per unit both result in increased feature densities, enabling powerful personal electronics, onboard chargers and small collaborative robot motor-drive systems.
Leveraging ultra-small ICs or highly featured chips can pave the way to smaller systems. For example, chip packaging options such as a wafer-chip scale package (WCSP) or an INA253 with an integrated shunt enables the designer to shrink the size of their system without sacrificing performance or features.
Conclusion
With a better understanding of these trends and the ICs that help support them, you can meet your specific high-voltage design challenges and enable reliability and safety by monitoring current measurements to ensure that the system is operating in a safe operating area.
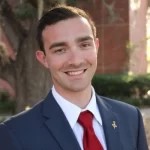