Fog and Industry 4.0 servers must provide high real-time performance on a small footprint. COM Express Type 7 server-on-modules enable space-saving servers with highly individual interfaces that can also be utilized outside server racks.
PC technology has been used for many years in machinery and plants for control systems and HMIs. Now server technology is following suit in becoming embedded as performance requirements increase in line with the challenges: Vision systems produce immense quantities of raw data that need to be processed and analyzed in parallel and in real time to realize visual and interactive robotic technologies. Connecting all this with other fog servers and Industry 4.0 machines and systems requires extremely high computing performance that can only be achieved with server technologies. It needs real-time Ethernet, superfast process technology, and ultramodern storage to efficiently handle the entire big data from horizontal and vertical communications.
However, before server processor technology can find a foothold in the control cabinet, some challenges have to be overcome. Above all, it is imperative to provide processor technology that is designed for use in industrial environments. This means it must be energy efficient because several hundred watts of processor power would produce too much waste heat for the technology to be usable in the industrial control cabinet. In addition, it needs to be available for a long time, as machines and systems have an operating lifespan not of years but of decades. Lastly, it must also be designed to support very different interfaces in the smallest possible footprint.
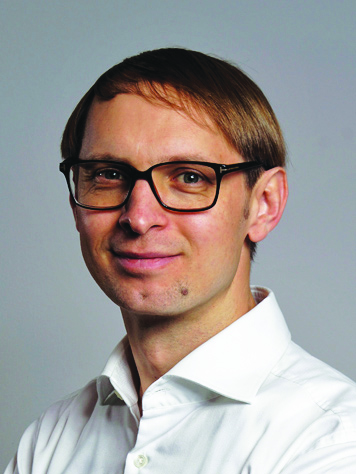
Marketing Engineer, Congatec
All these requirements can now be fully addressed by using standardized modules. Having proven themselves for many years in customer-specific embedded computer systems, they are predestined for extremely space-constrained Industry 4.0 server designs. For this reason, the PICMG has extended the COM Express specification to include a server-on-module specification: The COM Express Type 7 pin out, drafted by congatec as an editor. The first COM Express Type 7 modules currently offer two 10 GbE interfaces for horizontal and vertical real-time communication as well as up to 32 PCIe lanes for connecting the peripherals that can be used for fast storage media, General Purpose Graphics Processing Units (GPGPUs) and all types of industrial Ethernet interfaces.
The footprint of the COM Express Basic measures only 125 x 95 mm, which makes it possible to develop highly compact, yet extremely powerful mini servers. The first processor provided for server-on-module technology is the extremely high-performance Intel Xeon D processor (codename Broadwell) with up to 16 server cores, 32 threads and up to 48 GB DDR4 ECC RAM. Application fields for the new server-on-modules are found in industrial automation as well as in industrial big data storage and network applications. In particular, these include Industry 4.0 applications in cyber-physical factories as well as modular server designs for industrial cloud, edge and fog servers.
The application-ready modular core of the long-time available congatec server-on-modules offers a standardized footprint, carrier board interfaces and cooling concept, which significantly simplify system design, so new robust server technology can be introduced more quickly to the market. They also make future performance upgrades very easy and cost-effective, since all that’s required is a simple replacement of the server-on-module – even when the processor architecture has changed.
Since real-time support is key for many industrial fog and Industry 4.0 server designs, server-on-modules also support a software-definable pin for each of the 10 GbE interfaces. This physical pin can be configured as an input or output and is driven by the corresponding Ethernet controller. A typical application is the implementation of a hardware-based IEEE 1588 timing protocol for high-performance real-time applications to realize 802.1 timing and synchronization of distributed real-time systems, for instance to synchronize self-driving vehicles.
For application developers who also want to virtualize their server platforms, congatec has put together an application-ready bundle. It comprises the server-on-module, carrier board and a hypervisor from Real-Time Systems, which is particularly well-suited for industrial robotics, control systems and applications in the field of medical technology. congatec supplies this complete solution package also as a ready-to-run starter kit.
For such server designs, instead of SATA SSDs it is recommended to use SSDs that are connected via NVMe to the NVM Express or Non-Volatile Memory Host Controller Interface Specification – NVMHCI for short. This interface uses native PCI Express for the connection of mass storage devices, and COM Express Type 7 specifically supports this development by providing a large number of up to 32 PCIe lanes.
Starter kits to test the new server-on-modules can be ordered from congatec now. If required, the new Cloud API for IoT Gateways can also be included in the starter kit, allowing developers to implement communication via MQTT or other optional protocol standards. Rounding out the starter pack is congatec’s unique personal integration support – developers can enjoy personal contact for all needs and won’t have to wait in impersonal hotlines. As congatec also offers Embedded Design & Manufacturing Services for its server-on-modules, even complete customer-specific system designs including carrier board are quickly implemented without application designers having to worry about the details of the hardware design.